Sharon
Liu
Habitat's Airlock Linkage System
Mousetrap Car
Introduction to Mechanical Engineering, Fall 2018
For this project, I worked in a team of 4 to design and prototype a mechanically powered mousetrap car. The objective of the project was to create a mousetrap car that could traverse a curved track and stop inside a square parameter in the least amount of time over the course of 3 trials. Our team had two prototype designs which were considerate of weight and speed. In our final prototype, the car frame and the wheels were laser cut from ¼” thick plywood. The back wheels were tilted at a small angle toward the right. The mousetrap arm, wheel axles, and connecting axles were made using balsa wood dowels. To gain more traction on the ground, we used rubber bands around the wheels. We also tensioned our mousetrap with rubber bands in order to freely adjust and control the amount of tension in motion. Our final design featured an extremely lightweight body (300g) with larger backset wheels in order to minimize mass and optimize speed.

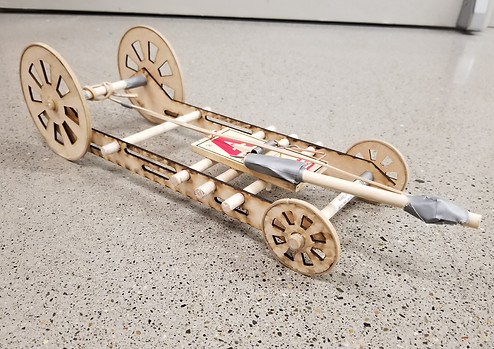
Testing Prototype
For the final prototype, we derived the angle by putting the track into a coordinate system. The motion of the car should be tangential to the circle so that the front axle should be perpendicular to the tangent line of the big circle. We laser cut a new right frame, so that the hole for the right axle was 1.5 cm behind the hole on the left frame. We also attached a long rubber band to the lever arm, so that we could cut some portion off if the distance traveled was too long during the trials. It was difficult to compute the length of the rubber band needed to travel the whole distance since we used rubber bands instead of string. The distance depended on the length of the rubber band as well as how much it was stretched. We intended to control the distance through a series of testing which would validate the length of the rubber band.
Overall, the mousetrap car had some sturdy qualities with parts that were easily reproducible and mendable in case something went wrong. For instance, we chose a simple design for the frame, which took very little time to laser cut. It was lightweight and didn’t take up much space on the vehicle. Instead of simply designing the frame to be a rectangle, we took into account some minor aesthetic considerations and added some edge to the vehicle: a triangular and a diamond shape at the ends of the frame. Another part that worked unexpectedly well was using the rubber band instead of a string to unwind the lever arm. We tensioned the rubber band so that it was extremely tight and was able to increase the elastic potential energy of the car, which caused it to transfer into kinetic energy for greater speed.
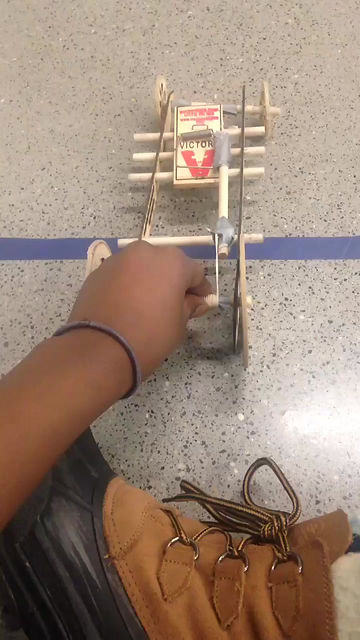
A chart of quantification of the vehicle’s performance

Design Iterations


Initial design for the mousetrap car where the wheels had bearings for maximized speed.
Final design for our prototype, the wheel bearings were removed because it would cause the car to move outside the square parameter, we also leveled the frame so that the rubberband could wind without interfering with the other rods.