Sharon
Liu
Habitat's Airlock Linkage System
Habitat's Airlock Linkage System
Engineering Design I, Fall 2020
For this project, I worked with a partner to design a robust linkage assembly system that can repeatedly rotate to press a button. The button simulates opening a Mar's backup airlock system for safety in order to prevent astronauts from being stuck in the Martian environment. The linkage assembly design chosen consists of three varying linkages of 1/4" thick acrylic held together by clevis pins and washers. The assembly is attached to two plated rigs and the middle crank link is attached to a motor which rotates nonstop for a period of 2 minutes. By creating and iterating on previous evaluative tests, the linkage assembly assures that there is adequate time for the airlock to open for astronauts to retreat back into the surface habitat safely. The system converts rotary motion to linear motion of which controls pressure in the airlock.
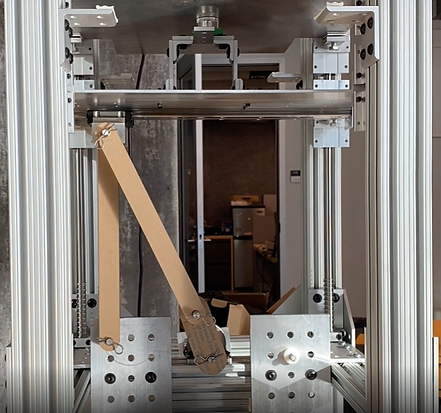
Linkage assembly on physical testing rig at maximum height position

Linkage assembly on Solidworks model

Testing Rig

Front view
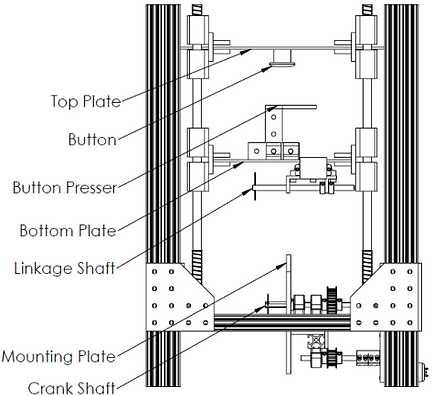
Right view

Isometric view
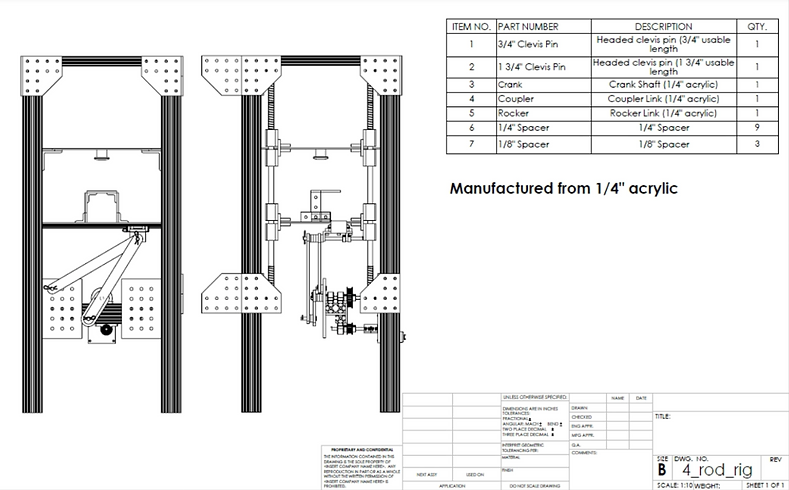
Bill of Materials and Drawing Assembly
Conceptual Ideation

Hand calculations and FBD of potential linkage ideations
In our ideation and selection phase, we tackled a few different ideas and their worst case scenarios. Then, we used a Motiongen simulation to analyze the arc of the traversed path. The first design was our ultimate choice for the linkage assembly. It was projected to have the most support, with the longest button press time.
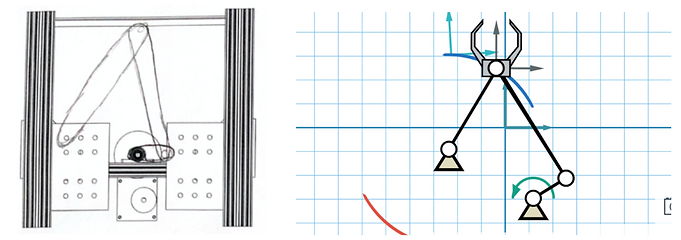
Concept sketch and motion gen simulation of assembly
Our linkage assembly successfully passed the closed button condition to sufficiently and safely open the airlock as simulated by the motor-rig system. We optimized the geometry of the links, in which longer links would increase the button press time, wider links would better provide structural support, and a thicker crank shaft would optimize rotary support. The goal of having the fewest long button presses, but the highest reaching height to maximize the timing of the presses was ultimately achieved.